On this page
Introducing four products of Prime Motion
InterMotion (Motion Controller)
Freely connect to a higher-level computer via Etthernet
Stand-alone motion controller
Three series to meet different needs
JOY-AMXGxx series
Only compatible with Panasonic RTEX servo driver. Connect to PLC via Ethernet. It has a built-in PLC connection program. Customers can operate the servo motor via Panasonic’s servo driver A6N, etc. simply by writing a ladder program of a familiar PLC.
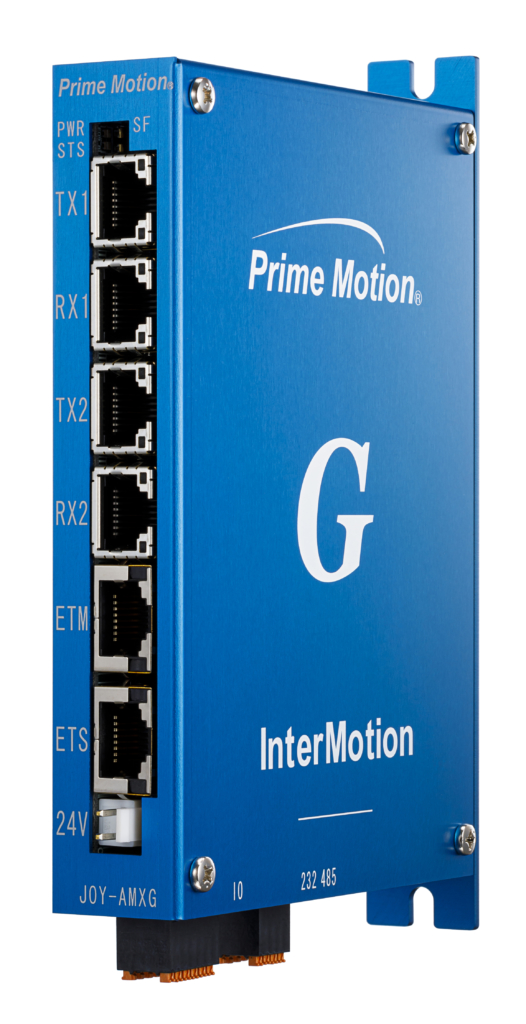
【standard products】JOY-AMXG16, 32, 64 *All products have the KC mark
Item | Specification |
---|---|
Number of control axes | ・16-axis, 1ms position command generation cycle ・32 axes, 1ms position command generation cycle(up to 16 robots), 2ms position command generation cycle (17 robots to 32 robots) ・64 axes, 1ms position command generation cycle (up to 16 robots), 2ms position command generation cycle (17 robots to 32 robots), 4md position command generation cycle (33 robots to 64 robots) |
Control method | Independent PTP movement, multi-axis synchronous PTP movement (up to 8-axis synchronization) |
Corresponding upper controller | Mitsubishi Electric PLC, KEYENCE PLC, OMRON PLC, Panasonic PLC |
Communication with the host controller | Ethernet, MC protocol by 100BaseTX, FINS command |
User program | Customer-prepared PLC ladder. No program development within JOY-AMXG16 is required. |
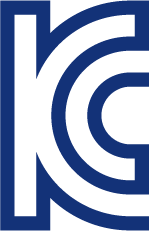
※KC mark:It is a national certification mark that guarantees the safety of products sold in Korea.
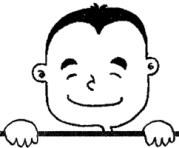
It’s spectacular to see 64 motors controlled by just one motion controller and moving!
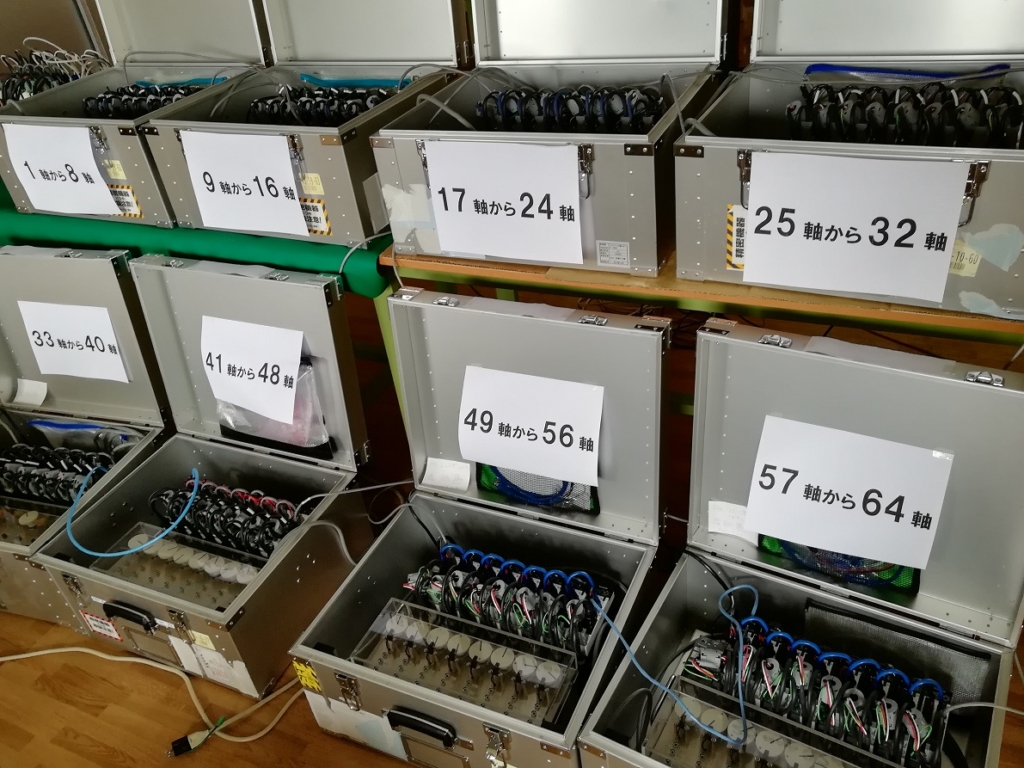
JOY-AMXGxx-WB series
Panasonic’s RTEX servo positioning. Ethernet connection to a Windows computer.
Customers can operate the servo motor via Panasonic’s servo driver A6N, etc. simply by writing a program in C # from Visual Studio.
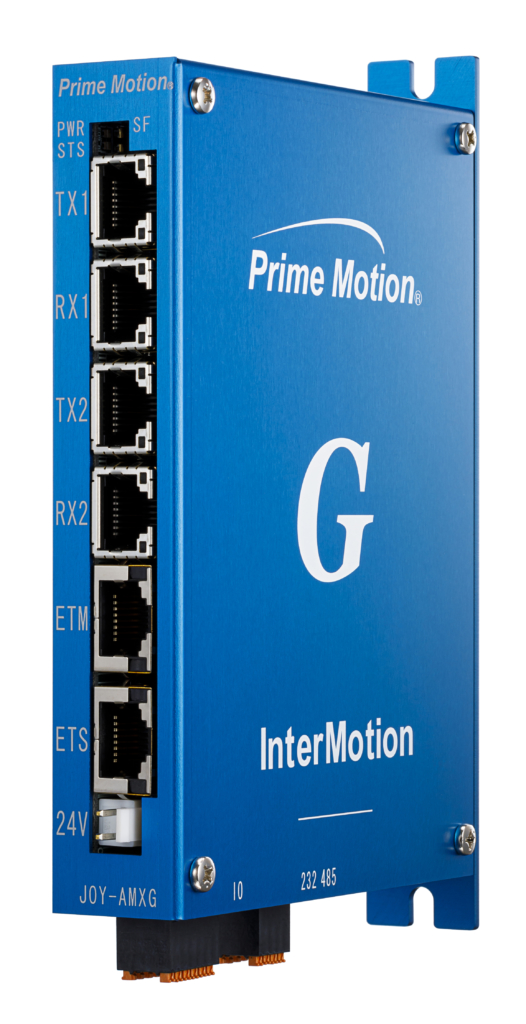
【standard products】JOY-AMXG16, 32-WB
Item | Specification |
---|---|
Number of control axes | ・16-axis, 1ms position command generation cycle ・32 axes, 1ms position command generation cycle(up to 16 robots), 2ms position command generation cycle (17 robots to 32 robots) |
control method | Independent PTP movement, multi-axis synchronous PTP movement (up to 8-axis synchronization) |
Corresponding upper controller | Windows10 PC 64bit |
Communication with the host controller | Ethernet. High-speed communication by 1000BaseT (Giga-Ether). TCP. .Net Framework library provided. |
User program | Windows application. No program development is required within JOY-AMX G16. |
JOY-AM8-WB
Pulse train position command 8-axis output. It can be connected to a servo driver and stepping motor driver for pulse train position command input. Ethernet connection to a Windows PC.
Customers can operate the servo motor via Panasonic’s servo driver A6N, etc. simply by writing a program in C # from Visual Studio.
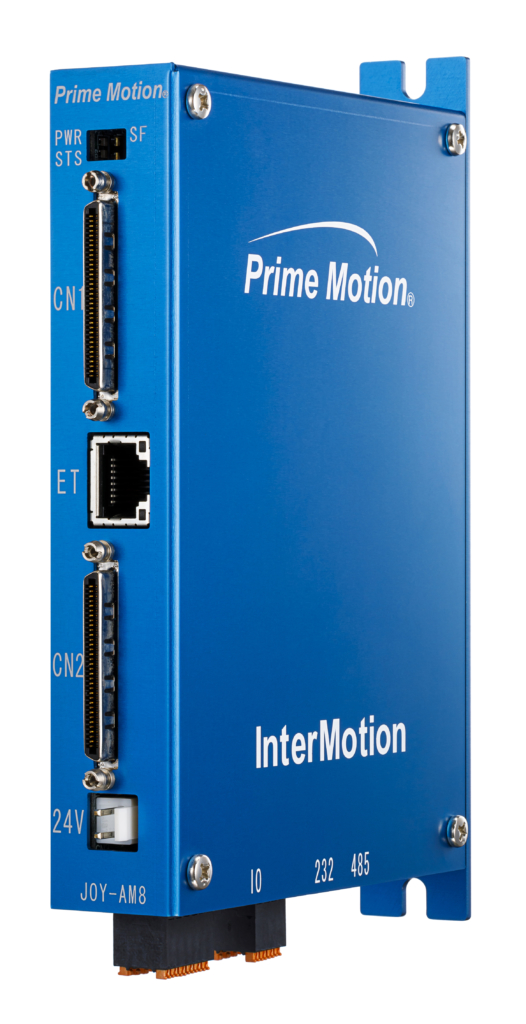
【standard products】JOY-AM8-WB
Item | Specification |
---|---|
Number of control axes | 8-axis 1ms position command generation cycle |
control method | Independent PTP move |
Corresponding upper controller | Windows10 PC 64bit |
Communication with the host controller | Ethernet. 100BaseT. TCP. .Net Framework library provided |
User program | Windows application. There is no need to develop a program with JOY-AM8-WB. |
Check here for more detailed specifications and prices.
Motion Card
A motion card that can be controlled in real time on Windows.
It comes with real-time extension software, drivers, motor control, and IO control runtime software.
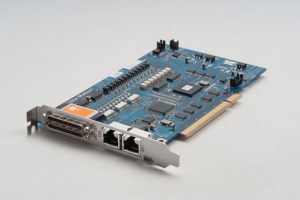
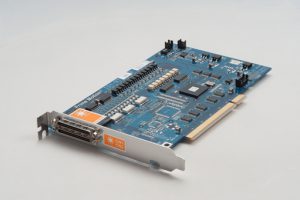
PCI card list
Function | Model | Remarks |
---|---|---|
Motion | JOY-RT40PR | 40-axis position command master RTEX 32-axis and 10MPPS pulse train 8-axis 8-axis AB counter |
Motion | JOY-RT40PR-PNP | 40-axis position command master RTEX 32-axis and 10MPPS pulse train 8-axis 8-axis AB counter PNP compatible IO |
Motion | JOY-RT8DR | 8-axis position command master 8-axis 10MPPS pulse train output 8-axis AB counter |
Motion | JOY-RT8DS | 8-axis position command addition slave 8-axis 10MPPS pulse train output 8-axis AB counter |
Motion | JOY-RT8DR-PNP | 8-axis position command master 8-axis 10MPPS pulse train output 8-axis AB counter PNP compatible IO |
Motion | JOY-RT8DS-PNP | 8-axis position command addition slave 8-axis 10MPPS pulse train output 8-axis AB counter PNP compatible IO |
PCI Express card list
Function | Model | Remarks |
---|---|---|
Motion | JOY-RT40PRE | 40-axis position command master RTEX 32-axis and 10MPPS pulse train 8-axis 8-axis AB counter |
DIO | JOY-IO6464E | 64IN, 64OUT |
MOS Bench PC
Real-time control personal computer
Real-time performance confirmed in Winndows10 Enterprise 2016 LTSB (x64) environment
Controllers for high-speed machinery for special equipment manufacturers
PM00217H series
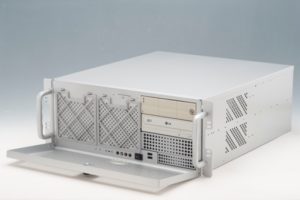
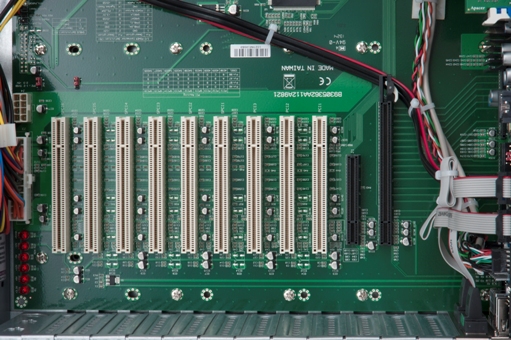
【Outline of standard specifications】
Item | Specification |
---|---|
Model | PM217H_2THDD2_06EJL |
External shape | 19inch 4U |
PCI slot, PCI-Express | 11 slots in total |
CPU | Core i7 3.4GHz 6th generation |
Main memory | 16GB |
Storage | HDD2TB |
Optical drive | DVD Super Multi Drive |
LAN | 2 ports (Windows control) * 1 Port can be controlled in real time |
USB | 4port(Windows control) |
COM | 2port(Windows control) |
Power supply | Nipron 500W |
PM00224H series (Mini tower size)
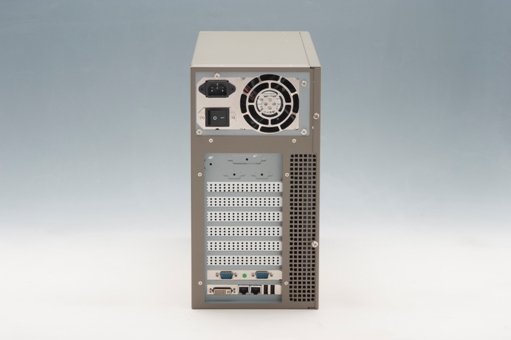
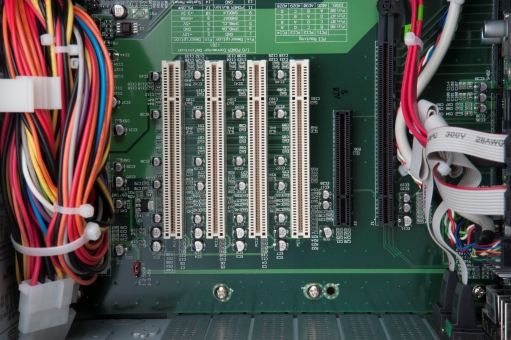
【標準仕様概要】
Item | Specification |
---|---|
Model | PM00244H_HDD_06EJL |
External shape | Mini-tower, floor-mounted metal fittings |
PCI slot, PCI-Express | 6 slot in total |
CPU | Core i7 3.4GHz 6th generation |
Main memory | 8GB |
Storage | HDD500GB |
Optical drive | DVD Super Multi Drive |
LAN | 2port(Windows control) |
USB | 4port(Windows control) |
COM | 2port(Windows control) |
Power supply | 500w |
Please feel free to contact us.
Program development environment
High-speed IO control and motion control with a 3.4GHz CPU.
Run 100 programs at the same time
This is a program development environment for industrial manufacturing equipment manufacturers and electronic component manufacturers in-house manufacturing equipment.
Four modules that make up the system
MOS Bench
It is an environment for efficiently developing programs in MOS language (C language-like machine control language).
After converting the MOS language to intermediate code, it can be executed in real time.
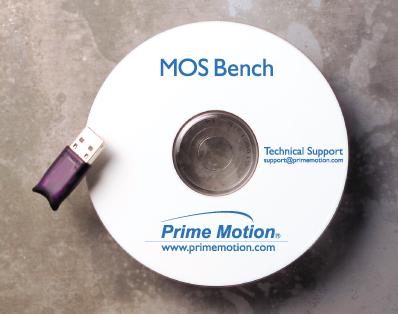
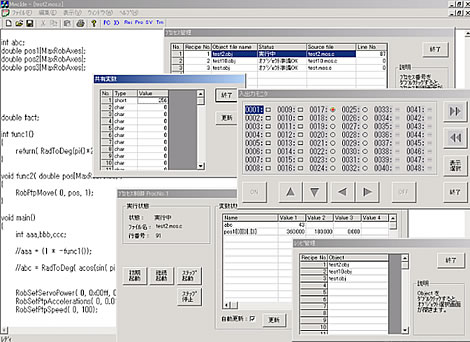
Main functions
Function | ||
---|---|---|
1 | Source editor | MOS program editing, execution trace |
2 | Process control | Start / stop each process, read / write variables, build, breakpoints, variable monitor |
3 | Shared variables | Read / write shared variables |
4 | I / O monitor | Physical I / O, Logical I / O Read / Write, AD / DA Read / Write |
5 | Standard output | Display the message output by printf () etc. of MOS programming language |
NwController(Multi-process controller capable of real-time execution)
It is a controller that can write MOS language and execute objects changed to intermediate code in multi-process in Windows real-time environment. You can execute multiple programs at the same time simply by registering the object you want to execute in the process number.
Easily multitask.
You can specify real-time interpreter execution from the following process management screen.
This screen has 4 multi-processes.
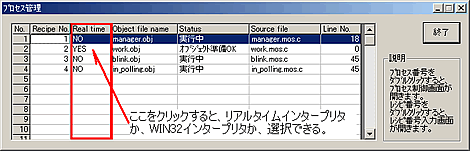
Feature
- High-speed execution (can be executed with a 3.4GHz CPU)
- Up to 100 programs can be executed at the same time
- 65536 shared variables between 100 processes and Windows applications
MOTIWARE
“MOTIWARE” is a software motion controller. Along with our RT series cards, it is possible to control the trajectory of complicated mechanisms that cannot be realized with a normal pulse train generation board.
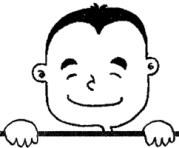
The main features of “MOTIWARE” are as follows:
・Trajectory control of complex mechanisms
・Independent control of up to 40 trajectories at the same time
・Up to 8 axes of synchronization
・Up to 40 axes, trajectory control every 1 ms
・Real-time control of DIO card, AD card, DA card, COM card
Main functions provided by MOTIWARE.
type | function |
---|---|
Arc interpolation operation | |
Perfect circle interpolation operation | |
Getting the final target position in the XYZ coordinate system | |
Getting the current position in the XYZ coordinate system | |
Acquisition of origin sensor status | |
Acquisition of servo power status | |
Acquisition of overrun sensor status | |
JOG operation in any direction in the XYZ coordinate system | |
PTP operation in XYZ coordinate system | |
Home return operation | |
Acceleration / deceleration parameter setting for interpolation operation | |
Speed setting for interpolation operation | |
Acceleration / deceleration parameter setting for PTP operation | |
PTP operation speed setting | |
Servo power ON / OFF |
Main items of configuration file
Item | Contents |
---|---|
Whole system | Actual machine operation mode / simulator mode |
Each mechanism | Number of constituent axes Mechanism mechanism Arm length |
Each axis | Presence / absence of encoder, number of encoder pulses Number of pulses per unit of movement of the axis Maximum pulse train output frequency Origin return method (origin sensor used, OT sensor used, etc.) Presence / absence of origin sensor, logic Presence / absence of overtravel sensor (OT) sensor, logic |
「RTX」runtime
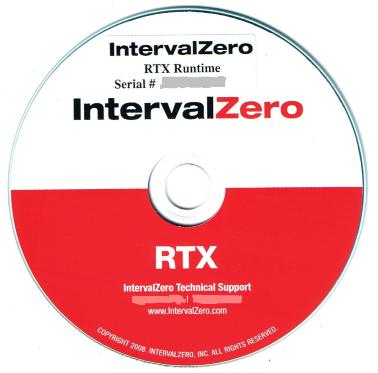
It is a tool for real-time expansion of Windows sold and developed by Interval Zero of the United States.
Windows-Installing RTX on your PC allows you to use your PC for real-time applications.
We will attach the RTX runtime license with our motion card.
Windows real-time control proposed by PrimeMotion.
Click here for more information
Contact
If you are having trouble with motor control
Please feel free to contact us.